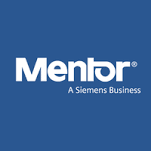
全球市场日益激烈的竞争格局,使得电子产品推陈出新的速度日新月异。传输一个好的产品模型,实现可靠高效的的制造投产流程,加快产品上市时间,可以有效提升企业核心竞争力。然而,现实情况却不容乐观,向制造流程传输产品模型的过程中,存在严重的效率低下问题。这是由于产品模型供应商只负责确定需要制造“什么产品”,但不负责确定如何“实现相关制造流程”。这就导致,加工、装配和测试要求等关键制造内容的缺失,给最终产品的投产上市带来极大的挑战。根据一家制造工厂的估算,大约25%的项目存在不同程度的数据完整性问题。
向制造流程传输设计数据面临巨大挑战
向制造流程传输产品模型的主要方法,是采用一系列不同格式的独立文件,每个文件用于确定及定义一个流程段的制造要求。其中Excellon文件表示相互间的机械连接信息,IPC 356文件表示电气设计意图,最常用的PCB裸板格式则是采用Gerber文件来表示各物理板层。通常,为了有效传递装配要求,还会提供非标准列表、物料清单(BOM)、合格供应商名录(AVL)和其他文件如:加工和装配文件等。采用这种方法向制造流程导入产品模型,会面临重重阻碍。对设计方案的重构会需要进行反向工程以重建产品模型的制造范围。而大多数CAM软件解决方案,为了确保满足制造准则,会要求提供某种形式的电路板构造信息或制造准备信息。此类信息要求众多且种类繁杂,这就导致每个步骤都容易发生错误,最终造成制造数据结果不完整或不一致。
在PCB装配流程方面,由于所需产品模型信息和设备制造供应商种类不胜枚举,因此即使要表达最基本的产品模型,也无法找出一种“近乎标准”的格式。缺少统一的标准,导致现如今的解决方案通常基于多种非标格式文件。PCB装配流程的CAM系统,也必须通过使用解决方案来读取这些非标准格式,从而尝试重建产品模型的装配表示。这样的处理,就给PCB装配流程增加了风险,也使得反向工程流程需要用到更多资源。
测试阶段,在多数情况下,设计人员会想方设法确保电路板设计为适当的测试留有余量。然而,目前用于传达此类关键信息的标准方法尚不存在。且制定可接受的测试策略,往往需要多个用户参与,这使得流程中的很多步骤,都会存在不必要的风险,可能会进一步导致测试程序未能面面俱到,或是未能在产品投产前及早发现测试过程中的可能存在的难题。
高效的产品模型是实现数据传输的基石
要想满足从设计流程到制造流程高效的数据传输,拥有一个高效的产品模型是极其重要的。此产品模型包含基本制造准备信息及后续相关制造内容。制造准备信息,是一个核心储存库,将过去使用的多个文件包含在一起,从而避免将层类型(信号、电源/接地、阻焊层等)和层位置作为产品模型,导致基本信息进行分配时,发生错误。制造准备信息,可以用来表示其他数据元素之间的依存关系,让其他CAM系统可以通过管理这些关系来改进生产效率。
产品模型,需要以全面的方式表达图形内容,且不受历史条件的约束。并且以智能的方式整理和表达基本产品模型,有利于产品模型的扩展,同时也避免了传统人工方式分配重要的制造要求。通过这样的处理,可以有效降低制造错误发生几率,避免严重后果例如产品报废、产品交付延期的产生。
正确的产品模型可以制定理想的装配机程序,但与此同时,理想的焊膏钢网也同样重要。焊膏钢网是制造流程定义的关键组成部分,它用于控制向各表面贴装位置喷涂的焊膏数量和形状。定义明确的产品模型,可以保持铜皮焊盘与每个元器件封装引脚之间的连接。
在最终的测试环节,产品模型应包含设计人员指定的测试位置。对于完整的产品模型,CAM系统可以自动扩大测试范围,帮助考虑设计人员的意图,从而最大限度提高测试质量。
ODB++助力充分实现PCB制造流程要求的最佳实践
如今,面对消费者日益增长的需求以及日趋激烈的市场格局,OEM厂商和供应商亟需实现以下目标。首先满足产品要求,降低成本。其次将生产进度延误降至最低,最后改善流程间的知识交换,提高制造流程的工作效率。现在,全新格局已经问世,可替代Gerber和Excellon等适用于低级任务的格式, ODB++格式支持加工、装配和测试环节中,从设计到制造的集成,还能保护产品设计的知识产权(IP)。与此同时,ODB++格式符合所有设计到制造流程的数据交换要求,在传输产品模型时,不但能够满足OEM厂商与供应商,高效、可靠数据交换流程的需求,甚至可能超出预期。在PCB制造流程的供应链环节,ODB++格式,可以让各方更多资金用于改善决定成败的关键任务和制造流程,充分实现PCB制造流程要求的最佳实践。
点击这里下载完整白皮书
来源:Mentor PCB及IC封装设计