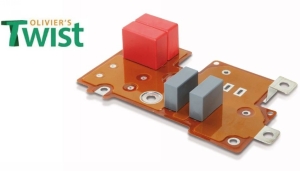
写在前面
ROLINX设计与开发团队致力于与全球e-Mobility原始设备制造商(OEM)合作开发下一代变频器系统,新的机遇不断涌现,新的要求也不能忽视:如低电感、可靠性、灵活的外形尺寸、遵循AEC-Q200标准等等,当然还有总的采购成本。为此,罗杰斯公司研发出ROLINX CapLink产品:一款完整集成了叠层母排和分立式电容的产品,目前已是客户的最佳解决方案之一。
背景
为促进e-Mobility市场发展,基于碳化硅(SiC)器件的动力系统应运而生。虽然碳化硅在系统层面上存在优势,但如果没有优化设计,这项新技术也无法被充分利用。更高的开关频率需要半导体器件和逆变器拓扑的双重优化来减少等效串联电感(ESL)并限制关断时的电压过冲,而直流母线支撑电容及其内部连接会显著减少等效串联电感。鉴于电容制造商提供的标准电容器型谱中的电感在20到30nH之间,如果客户选择了某种电容器或半导体器件,电感就固定了,没有了改进的空间。ROLINX CapLink的电感以nH为单位,通过差异化的内部连接和结构对产品进行优化。此外,还可通过软件仿真和特定的仪器测量在设计和样机试验阶段对电气性能进行预测。
鉴于e-Mobility应用的狭小空间,外形尺寸和结构是优化输出结果需要考虑的又一重要因素。与传统电容器组不同,ROLINX CapLink没有标准布局,在外形和布局上更为灵活。母排自身的形状或矩形或为圆形,非常适用于器件的动力总成,可极大缩小逆变器的整体尺寸。
▲ A:圆形ROLINX CapLink
▲ B:电容位于母排的两端
客户和供应商面临的另一大挑战则是可靠性,几乎所有客户都要求遵循AEC-Q200标准。完全达标为企业带来了沉重的成本负担。除此以外,企业还需要六到八个月的时间进行测试。尽管如此,罗杰斯的ROLINX CapLink解决方案集成了合格的AEC-Q200电容,满足最严苛的AEC-Q200要求,包括振动和热冲击。
客户也可以享受ROLINX CapLink带来的低总采购成本。如果客户想自己定制电容器组,工装和模具的投资也将是一个沉重的负担。举个例子,40×35×20mm(长×宽×高)注塑塑料外壳的模具成本在1万到1万5美元之间,而最小起订量是1万件。就这一点就让许多新启动项目望而却步。此外,ROLINX CapLink还可降低内部运营成本:单独采购母排和电容会增加组装和测试的成本。
在这个行业中,焊接工艺起初是为印刷电路板部件组装开发的,因此将电容和厚度在0.8mm以上的铜导体集成需要全新的技术。为实现焊接以及可靠的连接,ROLINX团队开发了一系列顶级的工艺流程,从激光焊接到波峰焊和机器人焊接,都可以处理厚度在0.6到2mm的铜材。此外,ROLINX凭借其在机械评估和电气测试上的经验,对所有ROLINX CapLink成品进行检验和测试(最高电压可达6 kV)。因此,客户能够享受到一站式服务,得到功能完善且经过完整测试的成品。
总而言之,ROLINX CapLink能够满足每位客户的定制化需求,拥有更加出色的电气与机械性能、通过量身定制的优化设计方案、更低的总体采购成本和更快的入市速度。ROLINX Caplink,不仅是电容和母排的简单相加,更是一种完全集成的解决方案。这就是1+1>2。
来源:罗杰斯先进电子解决方案