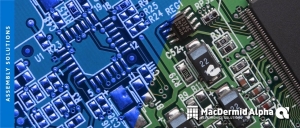
近期,在备受关注的IPC-TR-587 技术报告中,有一项关于三防漆的重要研究 -“三防漆材料和应用-行业现状评估”,研究结果概述了三防漆主要分类、涂层应用技术、涂层固化技术以及在常见元件表面上的最终薄膜厚度。IPC报告强调,适用的标称厚度并不能详尽代表三防漆材料在各种金属表面上的厚度或覆盖度。在许多情况下,薄膜厚度低于测量极限。在大多数的制造规范中,三防漆厚度被规定为组件的平坦无障碍表面上的最终聚合物薄膜厚度,但对其他组件和元件表面上的三防漆厚度却通常未予表征。
在该文中,我们比较了在分别涂覆最先进材料和和标准"行业现状"材料情况下的元件抗凝结性。实际上,该文的目的是为了更好地了解过去的假设如何反映现代、最先进涂层材料的现实情况,并为最终用户提供更为清晰明了的信息。
IPC-CC-830C概述了三防漆材料的性能要求和测试方法。测试是在由各种FR4和玻璃基材制成的平坦、清洁的测试试样上进行的。CC-830中未考虑工艺残留物、阻焊剂或元器件形态。虽然从材料性能规范角度而言这是可以理解的,但这也确实意味着该标准难以区分不同材料的性能水平。对阻焊剂的附着力、与工艺或免清洗残留物的相容性、以及对导电层(例如元件引线)的覆盖度、涂层对焊点寿命的影响、或焊点和引线对涂层材料热冲击性能的影响,均未写入鉴定文件,但这些内容却是三防漆在现实应用中的关键性能标准。IPC-J-STD-001按一般化学类型描述了可接受的涂层厚度范围,但这些仅涉及线路板上平坦、无障碍的区域,并不反映元件在最终应用中正常运行下去的必要条件。正如IPC TR-587所强调的那样,尤其是在考虑需要保护的金属表面标称涂层厚度和实际涂层厚度之间的差异时更是如此,如以下图1所示,该图显示的是一个典型元件的横截面,图中可见鸥翼元件弯头上的覆盖非常薄。
图1. 摘自TR-587的典型断面,凸显暴露的金属表面缺乏涂层覆盖。
在许多高可靠性的应用(例如汽车)中,通常在涂覆前不进行清洁,涂层和组装残留物必须能够适应预期的工作环境。工作环境中的组装工艺残留物和空气污染物会导致金属枝状生长,从而导致漏电,使得电路性能下降或导致电路组装过早失效。在实验中,使用国家物理实验室(NPL)的静态气室法将“免清洗” 表面贴装元件置于受控的冷凝环境中,将测试板的温度抑制在露点以下,同时测量表面绝缘电阻。
使用各种常见的应用方法,与"行业现状"报告中使用的方法相同,按照正常的标称厚度对6种不同的涂层进行涂覆和固化,并在检验样板上测量。基于其将各测试点表面绝缘阻抗值维持在广泛使用的100MΩ合格/不合格标准之上的能力,对这些涂层进行涂层保护指数(CPI)评分。在冷凝测试后,对每套涂层中的一块线路板进行了大面积横切,并检查涂层厚度和覆盖度,以了解厚度、覆盖度和内在物理属性是如何搭配决定涂层保护指数的。同样的6种涂层也应用于表面绝缘阻抗测试试样,并在有和无冷凝元件中所使用的相同回流焊免清洗锡膏情况下进行测试。表面绝缘阻抗在85°C/85%相对湿度条件下进行的1000小时实验中测量,这是汽车工业中经常进行的普通混溶性测试,用于了解锡膏/涂层混溶性对冷凝测试中获得的涂层保护指数的影响。
抗凝结测试由NPL实施,测试方法是让气室条件保持不变,并通过降低连接在压板上的元件温度而诱导凝结,在低于露点0.1到1.0m之间,于48小时内进行8次循环。
NPL元件上的每个元件类型都有一个与之相关的表面绝缘阻抗模式,在整个冷凝条件下连续测量表面绝缘阻抗,数据的典型示例如图2-4所示。
图2-4. 在冷凝实验中为双组分聚氨酯材料获取的典型表面绝缘阻抗数据。
基本而言,在整个冷凝循环中,结果保持在1000GΩ以上,没有出现故障。在冷凝阶段,绝缘电阻(IR)明显发生轻微下降,并随着涂层在循环间不断干燥时,略微上升。如果我们将这一数据与获取自性能最差材料(一种低粘度聚氨酯丙烯酸酯,旨在通过薄膜涂层技术进行涂覆)的数据进行对比,我们看到IR值存在明显变化,并且一些通道在干燥阶段未能恢复,因此意味着永久性腐蚀。
为了尝试对涂层性能进行排名,NPL设计了涂层保护改进(CPI)值,用于区分每种涂层的保护能力。
冷凝增加分为8个级别(1-8),每个周期持续6小时(总测试时间:48小时)。
如果在一个冷凝范围内,某个元件的IR值低于100MΩ,那么该级别就会被记录下来。由于CPI是一个改进值,必须从该值中减去无涂层元件失效时的级别,以得出改进值。本实验中,为受测试的涂层所确定的CPI值如表1所示。
表1. 受测试涂层的CPI值比较
在被认为"最先进"的材料,即在进行行业现状评估时尚未面市的现代无溶剂配方中,双组分UR和单组分SR涂层为所有受测试元件提供了涂层几乎可以达到的最高保护水平,尤其是QFP元件,而"行业现状"的溶剂型材料一般很难实现这样的保护水平。令人惊讶的是,低粘度的最新型LED可固化UV材料在整个线路板上的表现非常差,特别是在0402电容器上,相对于无涂层线路板,其性能没有任何改善。这些数值显示在图5中。
图5. 各种涂层的CPI值
如图6所示,当考虑CPI值时,单组分SR和双组分UR材料获得了完美分值,这毫不奇怪,尤其是看到QFP的厚度和均匀性时。不足为奇的是,URAR材料(图7)的CPI低于改良的SB SBC涂层(图8),这是由于URAR材料的厚度为零,而SB SBC材料的厚度为8µm。然而,令人惊讶的是,尽管覆盖度为零,CPI值却非零。在图7中,我们可以看到,零厚度的位置处于弯头上相当高的地方,这可以简单地归结为在最初的几个周期中冷凝不足,无法弥合引线和驱动故障。受测试的传统、行业现状材料的横截面也显示出与图8类似的趋势。
图6. 双组分UR涂层元件的QFP截面
图7. URAR涂层元件的QFP截面
图8. QFP SB SBC涂层元件的截面
对于这些材料,在对所有类型的元件进行冷凝测试后,腐蚀现象广泛可见(如图9所示),而对于性能较好的材料,涂覆后的线路板看起来没有变化。
图9. 使用传统AR和UR材料进行冷凝测试后所看到的典型腐蚀产品示例。
最后,使用了NPL的冷凝测试方法和同样的免清洗锡膏组装,评估三防漆覆盖和保护三维表面绝缘阻抗测试板上元件的能力。在使用最先进材料的情况下,双组分UR涂层和单组分SR材料均获得了完美的涂层保护改进(CPI)值,横截面分析显示所有元件的厚度和覆盖度都很高。为了尝试达到与新材料相当的厚度和覆盖度,配制了一种经过大幅改良的SB SBC材料,并涂覆3层。虽然这种材料无法在生产中使用,但其CPI值明显高于其他传统材料。正如易力高在最初测试中所预期达到的那样,双组分UR涂层和单组分SR材料的结果是完美的。涂层厚度和覆盖度都是无缝的,在冷凝环境中完美地保护了线路板。尽管其双倍涂覆厚度远远大于推荐厚度,但AR和UR材料显示出与行业现状报告中预期结果相同的覆盖度和厚度问题。在对所有元件进行冷凝测试后,出现了腐蚀产品。令人失望的是,一种市售的低粘度薄膜涂层UV LED可固化、URAR配方材料作为最先进材料也参与了此次测试,但在凝结测试中的表现却差于传统材料。尽管这种材料的UV固化速度很快,涂层平整度也很高,但元件边缘的覆盖度却非常低。
随着电子设备处于更恶劣的工作环境(包括更高的温度和冷凝环境)之中,对涂层材料的性能要求也变得越来越高,NPL测试结果可用作出色的、不折不扣的指标,指出市场上现有材料的性能不足问题。易力高的双组分三防漆提供更为卓越的保护,与封装树脂所提供的保护相兼容,并能实现边缘覆盖和保护厚度。双组分UR涂层和单组分SR材料都经过了一系列严苛测试,包括浸泡和冷凝测试,而NPL确认其性能是其他涂层所无法比拟的。
来源:MacDermid Alpha