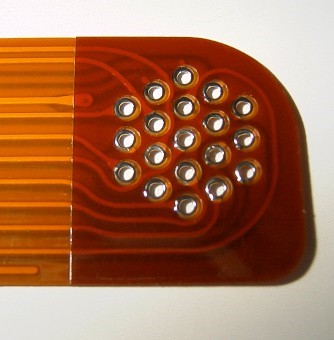
有许多连接器可能是专门为挠性电路而制造的,用于将挠性电路连接到刚性PCB上。许多产品使用典型的军用安全扭转连接器,这些连接器要求增强挠性电路以将其焊接到连接器引针上(图1)。另一个不错的选择是零插拔力(ZIF)连接器,适用于将薄挠性电路连接到刚性应用。此外可采用穿孔式连接器(图3)。还可采用插入刚性接插头连接器的直铜手指(图2)。
许多不同类型的连接器提供了成本低且可靠的方法将挠性电路连接至刚性PCB。然而针对挠性需要考虑的因素始终需要解决。检查弯曲半径,并可能需要在高应力区域中添加覆盖涂层增强材料。几乎任何可以在刚性PCB上采用的连接器都可以安装在挠性电路上。采用通孔式连接器(图1:焊接至军用连接器的增强型挠性电路),挠性电路应该在连接器区域使用FR-4增强板或在连接器的同一侧涂覆盖涂层来加强。然而当使用SMT型连接器时,应将更高硬度的增强材料,如薄FR-4,层压到挠性电路的另一侧,远离焊料面。
图2: 插入刚性PCB的指状挠性连接器
有很多方法可以将挠性电路端接和连接到刚性PCB上。最广泛使用的技术分为增强的凸形手指触点、非增强的凸形手指触点、标准通孔和表面贴装PCB连接器以及绝缘穿刺连接器四类。非增强的手指触点通常是除去绝缘层后的铜走线的延伸部分,或者是连接到电路走线上的较厚金属手指触点。铜手指可以弯曲成一定角度安装,也可以保持垂直安装。建议根据铜手指的尺寸、质量以及连接器的夹紧力,使用辅助支撑方法。可以考虑采用机械钳夹来限制连接器处的弯曲。在所有挠性电路应用中,必须考虑弯曲半径和挠曲性,以确保铜走线不弯曲,不能超过裂纹半径或弯曲循环次数。
必须考虑挠性电路连接可能在某个点上受到的应力。因为如果不能限制弯曲,就会导致刚性PCB上的连接器框架与挠性电路之间出现应力集中点,引起电路连接断断续续或完全断开。非增强的手指触点通常采用焊接方法,将手指直接插入镀通孔或焊盘中。非增强的手指触点通常采用热棒焊接工艺,以消除对连接器的需要。
厚铜镀金手指最常用于零插拔力(ZIF)或低插拔力(LIF)连接器。当在ZIF连接器应用中使用增强手指时,需要在图纸上指定必要的电路特性。关键项,例如手指区域的整体厚度以及电路边缘到手指的公差非常重要,因为挠性必须正确地与连接器中的窄手指配接。当挠性电路设计和制造适当时,ZIF连接器是低成本且可靠的选择。挠性膜或镀银膜与刚性PCB连接的另一种方法是通过各向异性Z轴导电胶直接黏合到刚性PCB走线上。
图3:挠性电路连接到刚性接插头的穿孔式连接器
绝缘穿刺连接器使用倒钩刺穿绝缘外层并与下面的铜导体接触(图3)。很多时候,弯曲的倒钩被焊接到挠性电路走线上以提高可靠性。绝缘穿刺连接器现在不太流行,而是更多地转向标准通孔和SMT连接。
采用通孔和SMT连接的PCB连接器是连接挠性电路最常见且成本最低的方法。通过利用D-sub或微D型等更常见的连接器,可以节省成本并确保供应稳定。可以为挠性电路设计或使用定制的PCB连接器,但是切记,定制的连接器成本可能很高,并且交付周期较长(通常为2~4个月)。对于挠性连接器,如果仅有一家供应商可能会产生致命的影响。
经验告诉我们,许多不同的连接器可能会有意想不到的问题,同时交期很长。明智的做法是检查供应商可提供的替代连接器和交付期。通常,连接器设计变化很快,应检查其他供应商是否有特定连接器的库存,以及会否因产量问题而被限制供应。
通常,在几乎每种产品设计中,挠性电路都是最后一个被检查和设计进系统的部分。设计师认为挠性电路是现成的,且是普通的部件。在挠性电路出现之前,典型的刚性PCB连接器很常见。为了防止将来在组装和部件采购中出现问题,在设计之初确定计划采用的互连技术至关重要,此时是定义和设置质量和可靠性参数的关键时期。需要粗略地设计挠性互连电路,定义连接器,并查看压力和挠性,这些因素都将在早期设计中起到重要作用。无论选择哪种方法,挠性电路制造商都可在选择过程中提供指导建议。
John Talbot任Tramonto Circuits公司总裁。如需阅读往期专栏或联系Talbot,可点击此处。