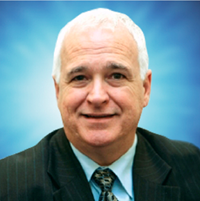
引言:与蚀刻相关的缺陷 上一篇专栏文章介绍了在最后组装阶段发现的问题。这类缺陷都是由电路板生产过程中的电镀铜引起的,只是在组装时才显现出来。本期的专栏文章将讨论两个有趣的技术缺陷。第一个是电路开路或蚀刻导致的,也包括与侧蚀相关的电路宽度减小。第二个是与板上的残留铜有关。这两种缺陷都说明了PWB故障排除和缺陷分析的复杂性。 在印制电路生产的蚀刻阶段出现的大多数工艺问题可以追溯到两个常见原因。蚀刻问题最常见、最明显的原因是蚀刻设备本身,可能是由于部件故障(喷嘴、压力)或调整不当,包括传送带速度。 在蚀刻步骤中,第二个最常见的原因是在先前的加工步骤中发生的问题,在电路板通过蚀刻机进行处理之前未被检测到。一个例子是在剥离电镀抗蚀剂时留在板上的抗蚀剂浮渣,可能导致不均匀的蚀刻。 另一个因素与化学操作参数的控制或缺乏控制有关。这些是未来专栏文章将要讨论的几种可能性。本文将要讨论的主要缺陷是由于蚀刻去除的电路走线和蚀刻后的残留铜。 由于蚀刻去除的电路走线 与裸板制造相关的最令人焦虑的问题之一是蚀刻后在一条或多条电路走线中发现开路(图1)。 图1:由于蚀刻去除的电路走线 (来源:RBP Chemical Technology公司幻灯片文件库) 当然,直到内层蚀刻步骤完成后,这种缺陷才显现出来。与此缺陷根本原因相关的可能性有几种。图2显示了被部分蚀刻去除的电路走线。 图2:由于蚀刻被部分去除的铜走线(来源:IPC) 该问题不太可能是由蚀刻工艺引起的,因为在电路板上只偶尔看到被部分蚀刻的区域。最可能的原因与铜表面的表面制备和抗蚀剂浮起有关,导致蚀刻剂接触到了底层铜。根本原因是抗蚀剂压合过程中,抗蚀剂未完全贴合铜表面。电路板上残留的水分可能已经蒸发,导致抗蚀剂在该点起泡。此外,研究了与铜箔相关的玻纤组织结构。厚重的玻纤织物可能会对抗蚀剂在该处的附着力产生负面影响。 残留铜 现在介绍另一种完全不同的缺陷。图3中的层视图显示了蚀刻后残留了多余铜(这是内层)。 图3:未蚀刻掉的残留铜 (来源:RBP Chemical Technology公司幻灯片文件库) 从广义上讲,这显然是一个显影-蚀刻-剥离(DES)的问题。但是,不要忽略对成像的关注。首先,作为故障排除规程的一部分,将实际蚀刻操作作为一个起点。只要看一下,就能断定电路板是蚀刻不足,但究其原因,需要检查蚀刻系统中的以下变量: 传送带速度太快 蚀刻液温度过低 喷雾压力下降的原因很多,包括喷嘴堵塞 所需化学添加剂补充不足 最后一个要点需要更深入的研究,这取决于使用的最终蚀刻工艺(氯化铜或碱性氨酸)。这两种工艺的具体特性将在以后的专栏文章中介绍。 在审查和调整蚀刻工艺后,应回到显影、表面制备和成像工艺。很明显,内层还残留着一些铜斑点。人们还可以在走线边缘附近辨别出外来铜。谨慎的做法是调查清洗前的层压、抗蚀剂压合、停留时间、曝光和显影。现在,重点放在显影上。 抗蚀剂显影不足 抗蚀剂显影不足将在铜表面留下残留的抗蚀剂,在铜表面起作用。当然,抗蚀剂膜厚度也会起到一定的作用。可以合理地推断,剩余的残留物很容易抑制蚀刻反应。未被蚀刻去除的铜其根本原因有以下几种: 显影液的工作温度过低:用手持温度计定期检查温度表读数 在显影液中的时间太短:虽然这在传送带模块中很少见,但仍可能发生。使用秒表或计时器测量在显影液中的时间 如果抗蚀膜断点发生了变化,是否意味着抗蚀剂在随后的试验箱中可能断裂或被清理干净?也许需要额外的时间。在显影液中需要额外的时间来改善断点(注:延迟的断点可能会导致不良的质量转移,以及喷嘴堵塞会影响如狭窄的抗蚀膜通道底部区域显影不完全,特别是在窄间距的走线之间会有残铜) 显影液浓度低:同样,检查pH值。在pH值为10.4至10.8的情况下,对大多数水性抗蚀剂显影效果都很好 不管怎样,如果显影操作由与pH值相关的自动进料和放料系统控制,应该不会出现显影不充分的问题。不过,抽查碳酸盐的pH值和浓度并没有什么坏处。 最后,要认识到防止抗蚀剂残留在表面上,否则将使显影更加困难。 在后续介绍层压和成像的专栏文章中,将对显影进行更详细的介绍。 作者:Michael Carano,RBP Chemical Technology公司技术和业务开发副总裁