小红蛱蝶的迁徙是从加州东南部沙漠到北部的阿拉斯加州(题图)。这种蝴蝶的翅膀只有2英寸至3英寸长,但它们的飞行距离却是如此惊人。
题图:小红蛱蝶(来源:Renee Grayson)
将智能PCB数据从设计传输到制造流程的整个过程与蝴蝶迁徙有什么关系?一只仅能在地面爬行的毛毛虫化身为翅膀上有独一无二图案的美丽蝴蝶,这个过程就好比将一个产品理念转化为原理图,然后再将原理图转为独一无二的PCB设计。其中的差别在于大自然已经创造了完美的衔接过程,但我们还很难做到重复使用同样的工艺来得到积极的结果。在PCB设计中,设计意图和制造过程需求的转化还尚未连接在一起。
ODB格式最初的目标就是为了满足这一需求(图2)。最初是PCB制造商开始使用这种格式,这样一来就再也不需要收集多种格式的CAM文件——例如Gerber 、Excellon、IPC-356甚至还有IPC-350,这些都是早期行业为了简化转换过程而做出的尝试。ODB格式之所以能成功,关键在于它获得了行业的认可。最初采用这个格式的是一个很友好的非正式小组,他们之前的想法是希望能用最少的数据处理量和有效、可靠、可以重复操作的方式迅速将有效的产品模型转化为能够交付的PCB产品(图3)。
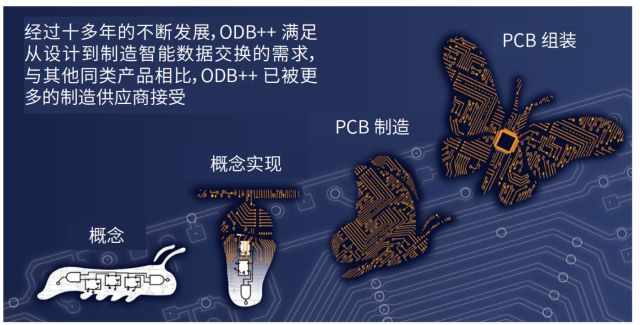
和毛毛虫化茧成蝶的过程一样,PCB从设计到制造的过程也是非常复杂的。当ODB格式中加入了组装信息以后,就形成了如今使用的ODB++,这一信息又增加了对ODB++格式的额外需求(图4)。2014年《Aberdeen Group Study》中强调了格式的复杂程度在不断深化,其中有44%的受访者表示PCB设计数据管理的首要难题是数据的复杂程度,其次便是在管理过程中整合这种复杂数据以及数据交换等。
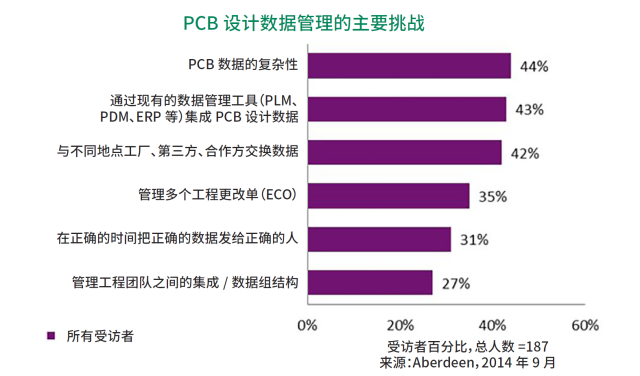
本文将探讨ODB++格式如何在20年前开始解决这些难题,以及ODB++格式如何继续在行业需求的基础上不断发展。不论是在过去还是未来,ODB++会一直对公众开放,支持行业因工艺不断发展和需求不断增多而产生的信息增加与变更需求。
当ODB刚刚问世时,设计的复杂程度还停留于4层至6层、线宽/线距刚达到8 mil的PCB,而且将所有层连接到一起仅需要一次钻孔。和如今的要求相比,当初的要求可以说是非常简单。但是到了2018年,4层至6层PCB的产值达到了大约155亿美元,而8层至16层PCB的产值大约是前者产值的一半(76亿美元)。渐渐地,我们确定了如何在4层至6层的PCB设计中加入更多复杂元素。这种做法需要制造工艺不断发展,因此,用于生产同一种设计的产品模型也必须要提升。
ODB是界定代表待生产产品的数字孪生品的基础。随着PCB设计复杂程度的不断增加,数字孪生品所需的数据也在以惊人的速度增多。主流的8层设计已成为了常态(至少对于部分设计而言),但与此同时,线宽/线距变成了6 mil甚至有时达到了4 mil,但生产面积却与之前的电路板设计保持一致甚至变得更小。另一种迹象是设计中铜走线的布线密度大幅增加,而所需的数据量也在以同样甚至更快的速度增加(图5)。
随着盲孔、埋孔、填充通孔和背钻孔的出现,钻孔工艺也变得越来越复杂,产品模型中也要加入相应的代表特征。曾经完全是刚性的PCB设计也出现了挠性PCB设计。之后又出现了刚挠结合电路板,单块电路板设计中的多个叠层区域同时存在刚性和挠性区域。制造工艺的组合数量似乎也是无穷无尽。
随着ODB++的采用越来越广泛,这种格式的支持者意识到了要在产品模型中加入与元器件相关的内容。这样做的最初目的是为了能够通过引入组装分析方案来检查元器件。后来,组装编程方案开始使用ODB++格式作为驱动贴装设备、设计焊料钢网和创建组装指南的基础。元器件复杂程度增加之后,ODB就变成了ODB++。做出这一改动后,ODB++产品模型就可以容纳来自单个独立来源的制造和组装内容。
如今使用的ODB++格式,其根源在于能够满足制造和组装制程中对数据的复杂性需求。ODB++不断得到改善,紧跟因制造工艺要求变化而导致的PCB数据复杂程度增加的步伐。
自Gerber 格式出现以来,能够满足PCB制造市场需求的最成功商用可行方案应该就是ODB产品模型。行业也尝试过提供一些可以超越ODB++的商用或行业赞助的其他方案。
例如有家赞助使用GenCAM格式的公司发布了多个IPC-25XX技术标准。这些IPC标准之所以出现是因为“GenCAM格式旨在提供CAD到CAM或CAM到CAM之间的数据传输规则以及与生产印制线路板和印制线路板组件相关的参数。”其中一种商用可行方案就是Ucamco推出了Gerber格式的更新版——Gerber X2。
如今,从设计到制造的主要商用流程之一就包括ODB++导入或导出方案。所有PCB设计、DFM、生产制造、组装市场内的主流方案供应商都可以在他们的应用界面直接使用ODB++产品模型,其中很多公司这样做已经有十多年了(图6)。
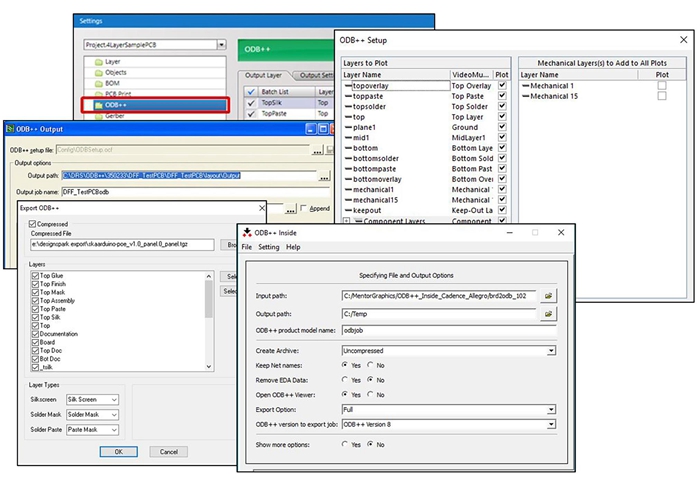
ODB++模型就是一组存储在一系列目录中的ASCII文件,每个文件都有明确定义的特定用途。在与其他方案集成的过程中,这一方法既有优点也有缺点。
ODB++涵盖无数目录中的多个文件,随后会用单个文件存档以供发布。另一种方式是使用包含了产品模型的单个文件,在发送给制造工厂的时候对文件进行压缩和传输操作。鉴于文件的大小,不论是使用哪一种方法,若想在应用中使用任何内容,对产品模型进行解压缩操作是必要的。使用单个文件的方法更简便也更不容易出错。但是不论哪种形式的产品模型,产品模型消费对于制造方案用户而言都是透明的,所以这两种方法在复杂程度上没什么区别。
正如前文提到的,产品模型的数据规模正在以惊人的速度扩大。日常使用的单个PCB产品模型就可达到200M。在其他应用中集成产品模型时,常常用结果的响应程度来衡量集成是否成功。当产品模型划分为包含用于特定目的的内容时,对集成的要求是只需读取完整产品模型的目标部分即可。这种做法缩短了应用的响应时间,并鼓励了对产品模型的进一步使用。其他方式可能需要一款应用来横向定位大部分数据,直到定位到被请求的数据。
例如要定位产品模型顶部特定元器件的参考标识符和产品模型内部指定钻孔层上的加工孔,在使用ODB++时这类信息会定位到两个更小的文件中:一个文件包含元件的位置,另一个文件包含钻孔的位置。而在使用其他格式时,这个集成过程可能就需要读取更多产品模型的内容才能获取相同的信息,而其中有很多都是不必要读取的内容。
与方案供应商以及当前ODB++使用者合作时发布到制造部门的数据越来越大,很多情况下,ODB++产品模型内容已经成为了其中的一部分。Bob Dylan曾经说过,“没有什么是比变化更加稳定的。”自ODB首次发布以来,设计和制造工艺发生了巨大的变化。如今,ODB++中的每个变化都会按照一套标准进行严格审核。
最基础的要素是格式发生的改变是否仍然能保持向后兼容性。ODB++格式能做到这一点,因为其数据结构可实现为指定目的隔离一个改动。如果改动并没有导致格式失去向后兼容性,那么这种改动可以进行更新或在同一版本号下发布次级版本。而那些影响到向后兼容性的改动则需要等到发布下一版本的ODB++中再进行。
为什么这一点如此重要?不论是与商业应用供应商集成还是由ODB++采用者完成的定制实施,至关重要的是通过产品模型的使用来实现可靠的时间表。当需要对格式做出改动时,更新区域要易于确定,而且改动方式对“从设计到制造”整个流程的影响最小。格式的开发已经确保了ODB++产品模型的发布不会影响到供应链上的任何合作伙伴。
ODB++是一组易于理解的文件,每份文件都有指定的用途。它确保用户能够从应用提供商甚至通过定制开发迅速获取产品模型部分。使用的规则由来已久,所以格式非常稳定,确保两次发布之间的兼容性保持稳定。ODB++产品模型的开放性确保了这种格式能够与其他制造管理应用系统进行集成。
出于生产的目的,以多种格式交换多个数据文件的传统方式通过定义需要生产的内容来通知供应商,但这种方式却没有定义如何完成制造过程。而ODB++却包含了必要的生产内容,可将制造、组装和测试要求发送给供应商。
有效交流产品模型的关键在于实现工艺的效率、提升产品质量水平以及缩短批量生产的用时,这也确定了产品的总上市时间。当使用ODB++产品模型来简化从设计到制造的整个过程时,生产过程中的很多步骤对新产品的成功发布都会起到一定作用。
ODB++模型能够让OEM与供应商在全球市场环境中保持竞争力,而全球市场不断寻求有效沟通制造要求的方式是取得成功的关键所在。多年来,几乎每个从设计到制造的行业软件供应商都将当前可用的ODB++产品模型支持纳入了产品的流程中。如今使用的ODB++产品模型已经得到了行业的评估、确认和采纳。
采用ODB++产品模型作为全面的数据交换方法可以让OEM和供应商更有效地:
在考虑采用产品模型时,应回想起毛毛虫化茧成蝶的过程,这是整个转化过程的主要目标。毛毛虫在模型内部构建了实现转化所需的恰当信息。ODB++产品模型完全代表了PCB设计,同时又可以满足定义制造过程的要求,从而可在没有任何中断的情况下,在规定时间内用最低的成本交付PCB。欲了解更多信息,可访问ODB++方案网站。用户与合作伙伴都可以免费注册获取ODB++格式。
标签:
#PCB设计
#概念
#产品
#ODB++