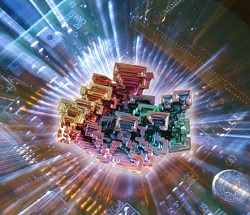
本系列的第3部分重点介绍Bi如何在这两个问题的答案中发挥作用,回顾第二部分请点击
为什么SAC不能成为电子电路的通用互连材料,为什么四元合金系统可提供更有效的方法? (注意: 本文提到的四元系统不包括掺杂有一种或多种元素的SAC)。
总体而言,SAC305已达到了预期效果——在大多数产品的运行条件下,能够为大多数(但不是全部)产品提供满意的焊接互连。 尽管如此,一些性能缺陷也如所料表现了出来。具体缺陷包括相对于SnPb合金的不良脆性(松散定义)以及可能发生焊点表面裂纹和其他与生产相关的缺陷和问题(如枕头形凹陷、焊盘坑)。
减缓SAC305松散脆性的直接补救办法是降低Ag含量,因而业界引入了低Ag SAC合金组成(例如,含有0.3%Ag,0.8%Cu的SAC0308)。 显然,低Ag成分合金降低了金属成本,也有益处。 但是,随着Ag含量的降低,所形成焊点的机械性能(屈服强度、拉伸强度和抗蠕变性)预计会下降。 在此讨论的Ag和Cu含量范围内,通常涉及更复杂机理的抗疲劳性也预计会随着Ag含量的降低而降低。
测试测量结果与预期一致。对于Ag含量(在0.5-1.5%Cu范围内)的影响,测试表明,随Ag含量的增加,直至约4.0%,合金的屈服强度和拉伸强度几乎呈线性增加,其塑性随Ag含量的降低而增加[1]。
总的来说,较低的强度与较低的Ag含量相关联,这符合冶金原理。在进行单次测试之前 ,合金在产品运行的一段时间内以大体符合预期的方式呈现(或未呈现)其性能时,是非常令人满意的。
再来看制造工艺,它会影响电路板组件作为整体的完整性,与SAC305相比,含有低于3.0%Ag含量的合金组成(SAC305)液相线温度增加了。液相线温度随着Ag含量的降低而增加,这几乎呈线性关系。 这也是预料之中的,因为近共晶组成SAC305基本上是SnAgCu系统内可达到最低熔融温度(217-220℃)的合金。
液相线温度的那几度增量是否重要? 答案是肯定的。
液相线温度的升高需要提高工艺温度,以在封装级或板级组件中实现稳固的互连。液相线温度的升高也要求PCB材料和PCB内部结构具有更高的耐热性。不管通过何种方法,组件中使用的所有材料和元器件必须具有较高的温度容限水平,以便与由较低Ag含量所决定的工艺温度同步。
应该指出的是,SAC305的液相线温度已经使组装温度达到了高端,以适应当前SMT基础设施下广泛的PCB设计。低于213°C的熔化温度更为理想和宽容,可提供更宽的工艺窗口。 避免“窄”工艺窗口是减少生产缺陷的先决条件。
行业内已经建立了包括供应链在内的SMT基础设施的具体约束条件。为了满足对电子器件性能不断提高的要求,三元合金(如SAC)预计不足以成为可靠的互连材料,以提供先进电子产品所需的所有特性和性能,特别是抗热疲劳性,以经受大功率元器件对焊点施加的应力/应变。其他三元合金系统同样如此。
在已知的SMT制造基础设施约束条件下(如操作流程、工艺温度)和生产电子产品的材料的物理和化学属性的要求(例如环境稳定性)下,三元系统不具备基本的微观结构和冶金基础以支持更高级别的焊点性能和焊点可靠性。
对于外形尺寸很小的电子产品,要求的功能越来越多、功率也越来越高,使焊点必须经受大量的循环热应力。这是自从20世纪90年代初期以来,我的许多专业开发课程和出版物中所述的设计四元合金的起源。
值得注意的是,设计SnAgCuBi系统的科学基础不是在SAC系统中增加一个元素(在本例中是Bi)。 相反,相反,它是一种整体性的材料创新设计平台,在考虑常见的焊点失效机理的基础上,采用了冶金原理的基础科学和工程学。换句话说,目标是减轻那些可能的失效机理,焊点通过在芯片级、封装级和电路板上充当电气、热量和物理通道,将强大的半导体芯片可靠地连接到外部,从而形成可靠先进的电子产品,在生活的各个方面我们都喜欢使用的电子产品。
关于作者:黄博士是一位国际商务女强人、国际演讲人、商务与技术顾问,她一直致力于自SMT技术及无铅电子的发展,是该行业的领军人。她曾荣获多项殊荣,曾入选《技术女性》的国际名人堂,曾入选美国国家工程院,被授予R&D-Stars-To-Watch和YWCA成就奖获奖者。她曾在洛克希德马丁公司,Sherwin Williams Co.,SCM Corp和IEM Corp.担任高级管理职位,目前是H-Technologies Group的首席执行官,负责提供业务、技术和制造解决方案。她同时担任国防部陆军研究实验室董事会评估主席、商务部出口委员会成员、国家材料与制造委员会成员、各种国家委员会成员、财富500强纽约证券交易所公司以及民间和大学委员会成员。黄女士还拥有多个国际领导职位。她出版了500多种出版物和多本书籍,并担任贸易、商业、教育和社会问题的演讲者和作者。 她获得了4个专业课程的学位,还完成了哈佛商学院执行课程和哥伦比亚大学企业管理课程。 欲了解更多信息,请访问www.JennieHwang.com